Splendor of the High Tang EraTri colour Pottery of Tang Dynasty
5 min readUnpractical Lead Glazed Pottery
Tang tri-colour pottery is a type of low-temperature lead glazed pottery. It is so named because it presents three basic colours, namely yellow, brown and green, and it flourished in the Tang dynasty. Actually, Tang tri-colour pottery boasts a variety of glazes, besides the three basic ones other colours include blue, white, black, and so on. Customarily, pottery which has one or two colours is respectively called single-colour and bi-colour pottery, while those with three or more colours are called tri-colour pottery collectively.
Tang tri-colour pottery belongs to an overglaze pottery, applied with harmful mineral paints such as lead, therefore it was mainly used as funerary objects or indoor displays rather than applied vessels for eating and drinking. Nonetheless, itsti1l played an important role in the social life of Tang. It was a lively fruit of the prosperous economy and culture of Tang by absorbing advanced techniques of Tang painting, sculpture and craft arts, and boast vivid forms and gorgeous colours. The thriving of Tang tri-colour pottery was also an epitome of the elaborate funerary customprevailed in the Han and Tang dynasties.
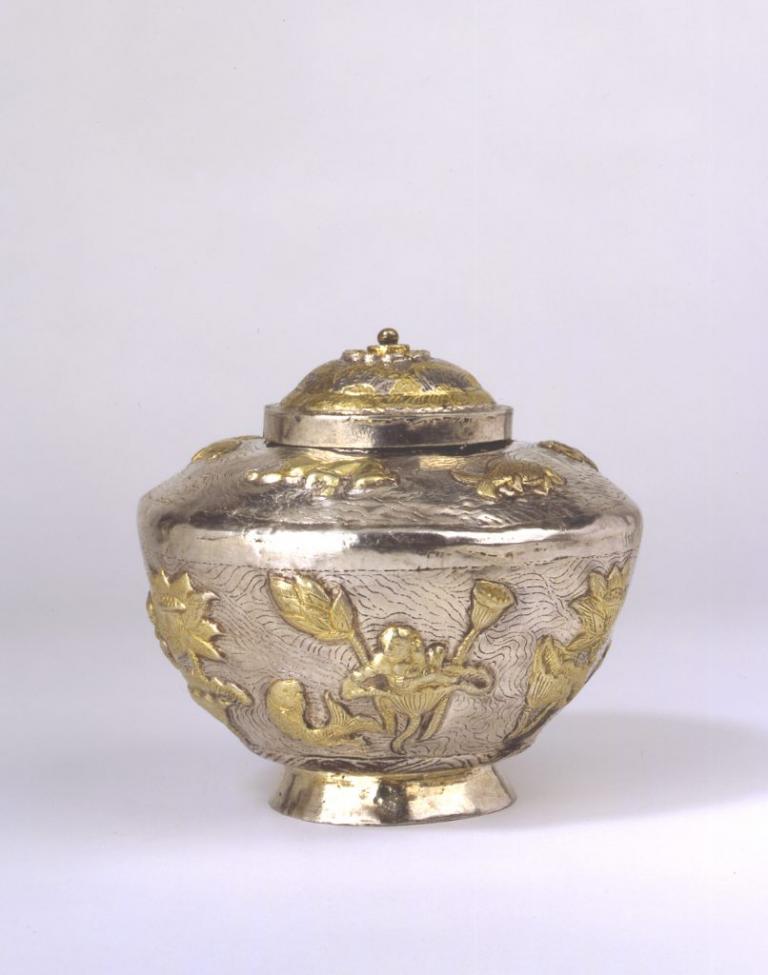
Tang tri-colour pottery was developed on the basis of techniques of low-temperature lead glazed pottery, which was extremely popular in the Han dynasty, and was especially applied for producing large numbers of animal figurines and models of granaries, wells and stoves in tombs. This kind of pottery was among the masterpieces of pottery craftwork of the Han dynasty, as well as in the entire history of Chinese pottery, and set the footstone for the emergence of Tang tri-colour potteries. Nonetheless, compared to the latter, its artistry is hindered by the monochrome application of glaze, especially green, which was usually thickly applied on dark colour greenwares such as red and grey, featuring poor fluidity and craftsmanship.
By the Three Kingdoms and Western and Eastern Jin period, the pottery industry was seriously affected by ceaseless wars during the time, and quality of potterywares gradually declined. Though production of lead glazed potteries continued,i was impossible for it to reach the height of Han either in quantity or quality. It was not until the Northern Dynasties, especially during the Northern Wei period, that pottery industry began to recover and flourish in the north again. During this period, production of lead glazed potteries was also improved on the basis of Han products. It expanded in application, and was even adopted in construction ofimperial palaces. The colour of lead glazed potteries diversified as well, as reflected by the yellow and green glazed basin found in Lou Rui’s tomb dating back to the Northern Qi period, which can be considered as rudiments of Tang tri-colour pottery.
The unprecedented prosperity of economy and culture during the Sui and Tangdynasties propelled the rapid development of pottery industry, which in turn enhanced the techniques for producing low-temperature lead glazed pottery. Variouscolour glazes such as yellow, black, blue, and production of marbleware (made by the mixture of white and brown clay to present texture of wood on finished products) took shape, while raw clay were selected more carefully. The technical requirementsfor producing tri-colour pottery were fully satisfied by then, and Tang tri-colourpottery finally came into being through repetitive experiments by artisans. Due to the lavish burial custom popular in the Tang dynasty, as well as the low cost of tri-colour products, they soon came into fashion and were made in large quantity.

According to archaeological findings to date, Tang tri-colour pottery wares were mainly discovered in high-level tombs in Xi’ an, the capital of Tang, Luoyang, the eastern capital and major cities such as Yangzhou, which are also the most exquisitetri-colour products, implying the fact that Tang tri-colour utensils were mainlyoffered to the upper class. Meanwhile, kiln sites for tri-colour wares are mainly located in Tongchuan of Shaanxi and Gongyi of Henan. However, due to the main function of Tang tri-colour pottery as funerary objects, traditionally it was considered inauspicious, and was deemed less valuable than funerary objects made of gold, silver, jade and other materials. As a result, people virtually knew nothing about it until late Qing dynasty, when it was mentioned by two Chinese scholars, Luo Zhenyu and Wang Guowei, in their works. Its artistic and historical value was thereupon cherished, and it became a treasure to collectors.
The making of tri-colour pottery was a very complicated process, such as careful selection of raw material, pounding, elutriation, sedimentation, kneading and fermentation. Kaoline, the same material for producing porcelain, was applied to produce a majority of Tang tri-colour wares, thus the fired bisques usually appeared white or primrose. Like ordinary pottery, Tang tri-colour wares were mainly producedby molds or wheels, while complicated larger ones were usually sculpted, which might probably be influenced by techniques of other craft industries of the time.
The main difference between Tang tri-colour pottery and ordinary pottery lies inthe different glaze and special firing technique applied, as it was usually firedtwice. The first was to fire the dried greenware with a temperature around 1,100℃Glaze was applied on the cooled bisque and it was fired again with a temperature around 900℃.A tri-colour product is considered successful if the glaze could melt during the firing process to present the mottled effect on surface of the product.
Though the process seems to be simple, it is very hard to grasp in essence, as the two firing temperatures should be well-controlled, so that the glaze could integrat well with the body and does not easily flake off.
When looking at Tang tri-colour pottery in a museum, people may notice a special phenomenon that most faces of tri-colour figurines are not glazed. The reason lies in the glaze-flow effect under high firing temperature. The mottling of glazes appears beautiful as body decoration, but a mottled face would be ugly. Therefore, faces of tri-colour figurines are generally unglazed, and would be processed after the two firing steps, which is quite similar to facial make-up today. White paint is first padded as the foundation, and then various parts such as mouth, eyes and eyebrows are delineated with corresponding colours to complete the production of a tri-colour product.
