Quality is Life
5 min read“Based on the current national specifications, the Xiangan Tunnel established a four-level quality assurance system: governmental supervision, judicial management, social supervision, and the enterprise self-evaluation.”Zeng Chao further said,”We were trying to form a multi-level, multi-faceted project quality assurance system in the implementation process of the project.”
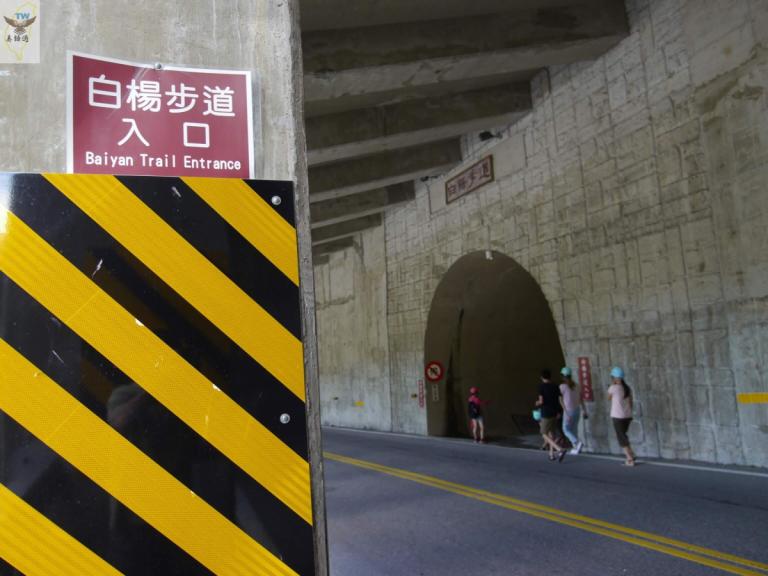
Standards are needed to assure the quality. After the domestic and foreign experts’ discussionperiod, the “Technical Specifications for Construction”,”Construction Supervision Outline”, and”Construction Supervision Outline Implementation Details”were completed. Under the guidance of the Quality Supervision Office,35 kinds of construction and supervision tables,121 kinds of quality testing tables,80 kinds of on-site construction record tables,11 kinds of measuring tables, and 44 kinds of testing record and report tables were developed. Systematic technical specifications on quality management and supervision processes were established.
Thorough management was ensured to in the Xiangan Tunnel construction. Any detail would not be neglected. For example, the constructors paid attention to the details like the joint parts between the tunnel wall decorative panels and the fire box in order to pursue the perfect unity of quality and aesthetics.
The management of common quality problems were reinforced in the construction process. The treatment, management and control of the on-site common quality problems were strengthened to avoid rework and potential quality hazards.
“We knew very well that any negligence could lead to a disaster in undersea tunnel construction, so we paid particular attention to detailed management. We carefully carried out the supervision and management in every process and every section, without overlooking even minor problems.”Wang Xuebin also said,”Especially facing the difficulties in the key construction technologies and the concealed work,I always went to the construction site, analyzed them and worked them out one by one in order to control the quality of the details, and provide a reliable guarantee for the project quality.”
Once, in an inspection just after construction started, Wang Xuebin found that some workers had cut a fixed length 4-meter-long bolt into half as a result of trying to cut corners. In line with the spirit of being highly responsible for the quality, he immediately ordered that all the bolts be pulled out. After he had checked the length of each bolt, he left the site, and at that time it was alreadydaybreak. This spirit of being highly responsible for the construction received positive responses from the construction units, and they all further strengthened the quality management awareness.No such circumstance ever happened again and quality awareness became deeply rooted in the hearts of the constructors.
Considering the electromechanical engineering in the tunnel was completed by connecting large amounts of hardware and software equipment together,the selection of types and materials ofmajor equipment was essential for electromechanical engineering quality.The owner units and supervision units required the carrying out of on-site supervision work for major equipment in each electromechanical section,and the contractor self-inspection system and the supervisor spot check system were strictly implemented.These methods not only ensured the quality of the main equipment and materials during the implementation of the project,but also effectively ensured the quality of the electromechanical engineering in the tunnel.
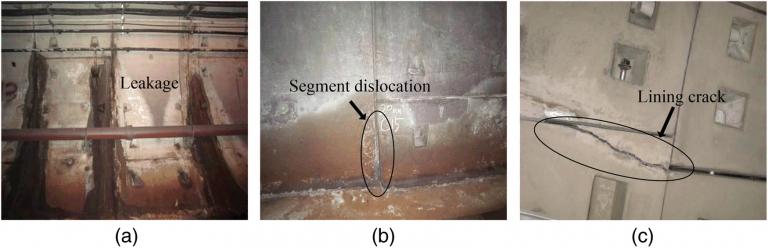
“According to its construction specifications,the Xiangan Tunnel will last 100 years in the undersea corrosive environment.”Wang Xuebin went on to say,”Since the tunnel goes through the undersea area,its concrete structure will be affected by the seawater’s vertical permeability,which has a weak corrosive effect on the rebar in the reinforced concrete structure,and moderate corrosive effects on the steel structures.”
In order to meet the design requirements,the mix proportion of the lining concrete used in the tunnel was preliminarily designed by Nanjing Hydraulic Research Institute.After laboratory testsand analysis of the results,a mix proportion based on their theory for suitable concrete was put forward.According to practical engineering applications,all the performance indexes met the requirements in design and construction after testing.Later,the constructors conducted research into the mix proportions with tens of different materials,and then selected the economic high performance concrete mix proportions which were suited to the characteristics of undersea tunnels.This ensured project quality and also protects the investment which has gone into the project.
All the construction units agreed that,so long as they ensure the quality and stability of materials with no rework,they can save on cost.Therefore,they put emphasis on the control ofmaterials during the cost accounting.For example,in order to control the waste of commercial concrete,they invested 80,000 Yuan to set up a weighbridge,which effectively dealt with the problem of properly measuring the concrete,cement,diesel and other materials,directly saved on costs.
In the Xiangan Tunnel, the “anti-seepage and anti-corrosion high performance concrete”greatly enhanced the lifetime of the tunnel. The anti-seepage grade of this concrete, which had been specifically designed for the undersea tunnel, reached S12 on the concrete permeability index, while the anti-seepage grade of national urban architecture only reached S8. Meanwhile, it also adoptedthe concept of “subarea waterproofing”using specific waterproof board placing. Each 10-m section was set up in such a way that any water seepage would be contained within a 5-m area, which would avoid wider ranging water seepage.
Under the “subarea waterproofing”concept, other auxiliary waterproofing methods were formed. Based on the desire for rigorous waterproofing methods, Xiangan Tunnel also designed anembedded grouting disk on the waterproof board. If there was water seepage found when using of the tunnel, the grouting could be conducted through the grouting disk for solidification. After the experts saw the waterproofing scheme, they said that the tunnel was “just like an iron bucket”. It was called the “most rigorous waterproofing”that could be carried out by the expert group.
Meanwhile, in order to monitor the effect of using concrete, and to monitor the long-term corrosion in reinforced concrete structures, the constructors also used embedded corrosion sensors in the tunnel construction. They used the Danish Force Company’s Corrowatch multi-probe corrosion sensors, independently researched and developed electrochemical corrosion sensors, and physical corrosion sensors to constitute a “high-low combining framework”, which allowed for areasonable corrosion detection and monitoring system to ensure the long-term stability of the tunnel.
It was reported that the reinforcement corrosion long-term monitoring system used in Xiangan Tunnel was the first large-scale reinforcement corrosion detecting system established in China’s tunnel projects. The number and the variety of the sensors embedded had created a record in China.They had formed a reasonable corrosion detection and monitoring system to ensure the long-term stability of the tunnel.
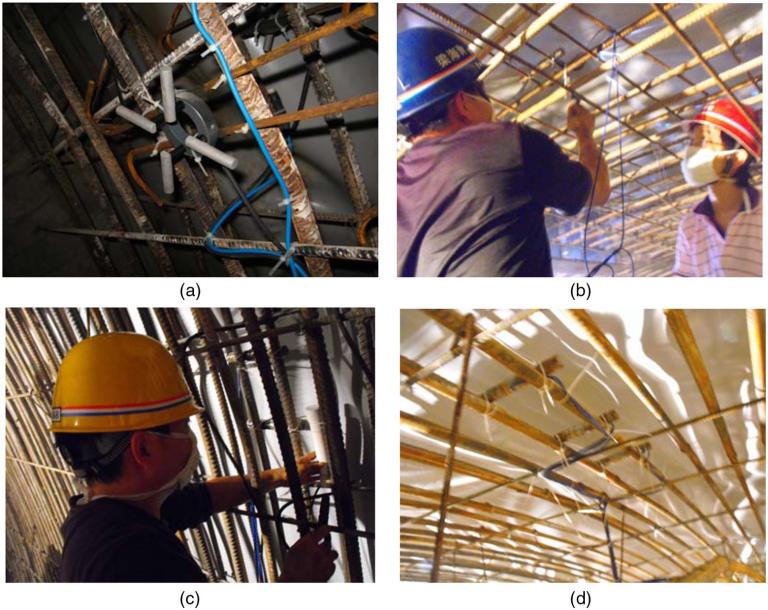