Chinese Ceramics
21 min readThe emergence of pottery ware was an important symbol of the neolithic Age Pottery ware made from clay can be classified into red, grey, black and white pottery ware according to bases colors. the main methods of making bases include molding mud strip winding and wheeling Molding is suitable for small utensils with irregular shapes; the mud strip winding method can be used to make larger utensils, but the walls of bases are thick; the wheeling method includes fast wheeling and smallwheeling. Fast wheeling(shaping bases with a pottery wheel) emerged late(around the mid-Neolithic Age). It could make utensils round and neat, produce evenly thick walls of bases, and improve productivity. Pottery ware’s burnt temperatures are generally 800-1,000C. At first, pottery ware was burned on the ground, but the temperature was low; later, high-temperature kilns emerged, capable of making utensils more solid. After a semi-product was shaped, it was often polished or coatedThe main decorations include paintings, impressions, affixations, carvings, etchings,Painted pottery basin with a pattern of human faces and fishes, Neolithic Yangshao Culture, made of fine red clay, 16.5cm in height and 39.5cm in diameter, unearthed from the ruins of Banpo in Xi’ an, Shannxi Province, kept in the National Museum of China. There is urn custom in Yangshao Culture, i.e. the children died are buried in the urns. this basin is the cover of the urn Colored pottery emerged in the late Neolithic Age and was the most famous pottery ware then patterns were first drawn on semi-finished products with reddish brown, black and white mineral pigments, and then they were burnt in kilns. Different from colored pottery burnt first and then painted with color in the Spring and Autumn Period and the Warring States Period, the patterns of colored pottery did not fall off easily after being burnt. Colored pottery is well decorated with abundant patterns, including the four main types of animals, plants, figures and geometrical shapes. Geometrical patterns are most numerous, while the most controversial decorative animal patterns such as fish, birds and frogs have clearly utilitarian color nstead of purely aesthetic
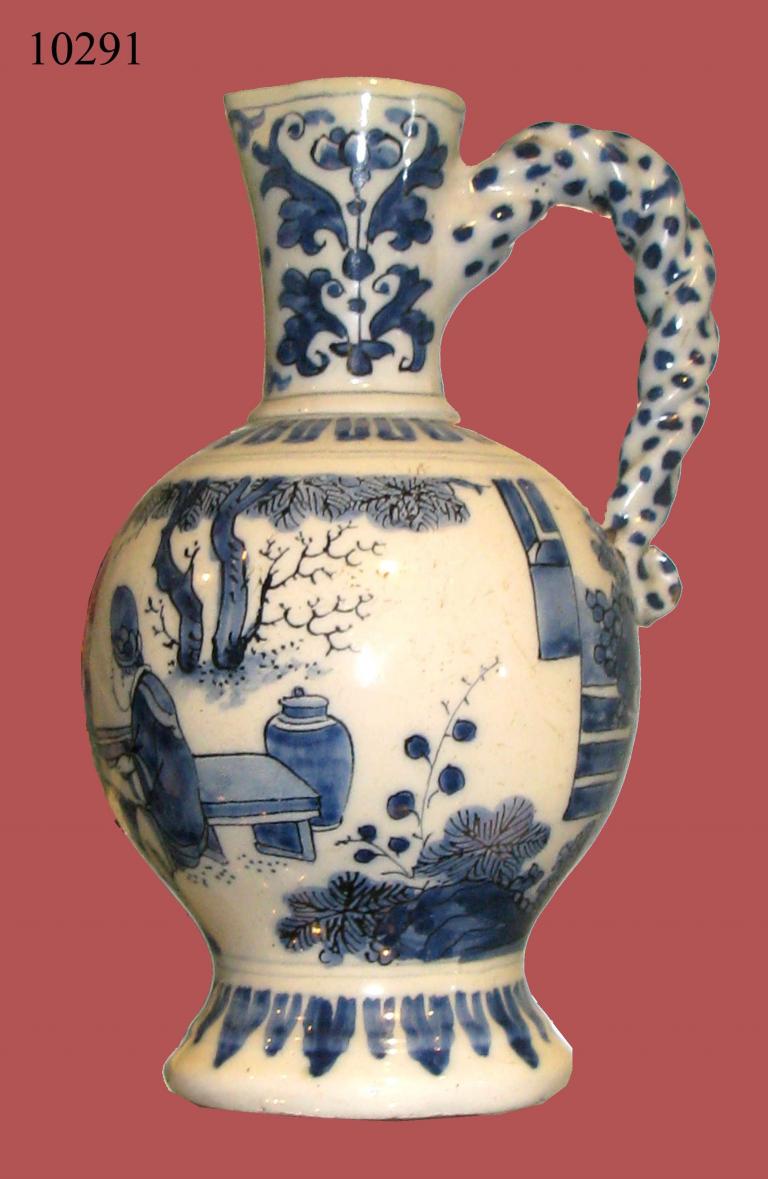
Colored pottery was widely distributed and the colored pottery of the Yangshao Culture and Majiayao Culture was most developed. Back then people mainly sat on the ground in daily life and utensils were mostly put on the ground, so colored pottery’s decorations are often on the most visible upper parts of utensils and inner parts of basins and dishes, and patterns also change when viewed from different perspectives such as the downward perspective and the sideways perspective
Black hollow-out pottery cup with fine handle and high foot, 26. 5cm in height, Longshan Culture, kept in handong Provincial Museum. This black pottery is made of fine clay. Although exquisitely made, it is not practical as the foundation is too small and the center of gravity is at the upper part.
Black pottery thrived in the Dawenkou Culture(4, 500 to 6, 400 years from now)and the later Longshan Culture in the lower reaches of the Yellow river. Bases shaped through wheeling were very thin the thickness can be less than 0.5 millimeters, so it is called “eggshell pottery. Bases of black pottery were greyish black and undecorated, so they excelled in shape. Utensils have neat and vigorous shapes, light and th bodies, shiny appearances, ears for reeving or affixing handles, etc most decorations are etchings or fine carvings
After long-term production and accumulation, primitive pottery ware’s shapes sizes and proportions conformed to scientific laws. Primitive pottery ware’s main shapes are extended, cut or compressed spheres, because spheres are large in volume, save materials do not deform easily in burning and do not damage easily in use Pottery ware’s sizes also conform to ergonomics, e.g. basins opening diameters are mostly 30 centimeters, shorter than man’s shoulder width and suitable for people to hold and move them in their hands bowls and earthen bowls opening diameters are usually about 15 centimeters, and the opening diameter, height and bottom diameter are usually in the proportion of 2: 1: 1, which is conducive to stability and similar to the current proportion

Primitive porcelain ware first emerged in the Shang Dynasty. The glaze was dark green and a little yellowish brown in color but the treatment of its raw materials and the refinement of clay were still quite rough. In the late Eastern Han Dynasty, porcelain production techniques entered a mature stage, the burnt temperature reached 1, 300C, glaze was combined with bases more tightly, and porcelain was moretransparent and less absorbent Porcelain ware with its good quality became more and more important in daily life, and ceramic production techniques thrived in a long time and developed continuously. The Yuezhou kiln in Zhejiang became the center of celadon production. In the Wei and Jin dynasties, people pursued pure, elegant, spiritual and fine aesthetic tastes. The flourishing of celadon in this period was just a manifestation of this aesthetic view. the area of celadon burning further expanded Some porcelain kilns applied makeup soil(mud of repeatedly elutriated white porcelain clay with low iron content and refined texture) to bases to make products of low-quality materials look better. This practice was extensively adopted for mid-and low-grade products in later ages
In the late northern dynasties white porcelain was burnt successfully in the north This was related to northern minority ethnic groups worshipping of Shamanism and admiration of white. White porcelain not only became a new type of Chinese ceramics, but also provided an ideal glaze color for later colored painting decorations. In the Sui and Tang dynasties, social prosperity and thriving trade pushed forward the porcelain production industry’s progress, expanded the porcelain production area and market and formed the pattern of “celadon production in the south and white porcelain production in the north: the south mainly produced celadon, the Yuezhou kiln in Zhejiang was the most representative one, porcelain clay was thin and dense, and the glaze was mild like jade; the white porcelain of the Xingtai kiln in Hebei was a representative of northern white porcelain “porcelain clay was solid and dense, the color was snow-white, and it produced metallic sound when knocked Secret-color porcelain was tribute porcelain burnt in the Yuezhou kiln in the late Tang Dynasty and the northern Song Dynasty. The glaze color was mild like jade, showing the new air of ceramics like ice and jade
Tri-colored glazed pottery with a design of dancing tomb figures on a camel of the Tang Dynasty, 66.5cm in height, kept in the National Museum of China. The barbarian culture pervaded the Tang Dynasty when the tri-colored glazed pottery was popular and this work is a real evidence of the cultural exchange. The two humped camel with five people(three barbarians and two Hans) on its back is a breed from Central Asia The yellow and green colors are traditional colors of the Han nationality, the cobalt is from Persia and the white color is a traditional color of the northern ethnic groups.
Ceramic shapes were thick and large in the early period of the Sui and Tang dynasties, and were thin and small in later period; most ceramics were burnt in saggers to ensure utensils smooth surfaces. The Changsha kiln was famous for colored painting and simple but vivid decorative graphics, marking the beginning of a new era of Chinese colored ceramic painting. The trio-colored glazed pottery of the Tang Dynasty was low-temperature lead glaze pottery burnt twice. Semi-finished products were first burnt at high temperature, then glazed and burnt at low temperature. there were many types with dazzling colors and most were burial objects. The shapes had a strong northern flavor, and cobalt pigments came from Persia and were closely associated with the West. In the Tang Dynasty, new types such as floral porcelain and porcelain with twistable glaze were invented. The former had light-colored random spots of various shapes on dark-colored glaze with natural charm the latter imitated Western glass mud strips made of white and brown or white and black porcelain clay were twisted, directly shaped into semi-finished products or cut into slices, decorations were affixed to the utensil surface and it was glazed and burnt at last. In the Tang Dynasty and the Five Dynasties, famous kilns stood in great numbers, a lot of ceramics were exported and exerted great influence.
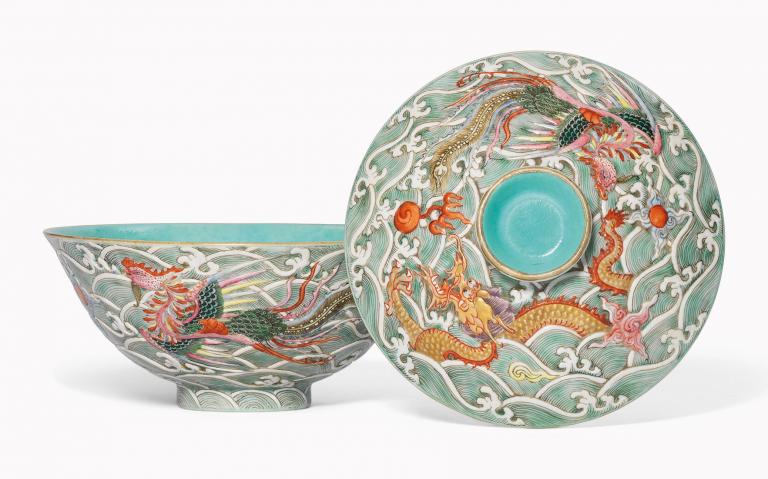
Black porcelain Yaobian cup, 12cm in diameter, made by the Jian Kiln in the Song Dynasty, kept in the Seikado Bunko in Tokyo, Japan. Tea competition was very popular in the Song Dynasty and the black glaze is the most appropriate for tea competition. For cups fired in Jian Kiln, the glaze is thick, the black base is often exposed at the bottom and there are often crystal stripes on the glaze
The Song dynasty was a golden age for Chinese ceramics. Emerging kilns were numerous, especially in today’s Henan and Zhejiang. Porcelain production techniques were consummate, shapes were regular, makeup soil was applied generally, and lime alkali glaze was invented to thicken glaze layers and create jade-like textures. Kilns were improved, and fire thermometers were used, making kiln temperatures and burning environments more controllable. The upside-down burning method was promoted, and the rate of finished products rose greatly. At that time, the local tribute system allowed the emperor to take possession of many classics from private kilns for free, and the imperial court plundered classics from private kilns through monopolizing purchase and sale, designating kilns and dispatching people for selection. The 20-80 split system in the mid-Song Dynasty and continued to be used in the Yuan Dynasty. The private mineral industry, including the porcelain industry should give 20% of products to the imperial court. Therefore, products of government-run kilns and private kilns were related in many ways. The so-called”five government-run kilns of the Song Dynasty”is only a vague term that emerged in modern times
Many famous kilns emerged in the northern Song Dynasty and the Southern Song Dynasty. Their unique styles led to imitation by people from far and near. The special products of the dingzhou kiln(in today’s Quyang Hebei) included milky enameled porcelain with exquisite carvings and patterns and purple dingzhou porcelain”witl purplish red glaze. The upside-down burning method was also invented and rough basin and bowl openings were decorated with sheet metal. bluish white porcelain from the Jingdezhen kiln was crystal-clear, deeply influenced by the dingzhou kiln Porcelain with black backgrounds and white patterns and porcelain with pearl backgrounds and carved patterns from the Cizhou kiln (in today’s Ci County hebei)had strong local flavor Celadon with carved and impressed patterns from the Yaozhou kiln(in today’s Tongchuan, Shaanxi) was clear-cut, sharp and natural Flambe glaze from the Junzhou kiln(in today’s Yuzhou, Henan) was a riot of color withpurplish red spots formed by copper glittering on blue glaze Celadon from the Ruzhou kiln(in today’s Baofeng, Henan) and the government-run kilns(in Bianjing, the Northern Song Dynasty and Lin’ an, the Southern Song Dynasty, i. e. today’s Kaifeng, Henan and Hangzhou, Zhejiang) was slightly blue, and the glaze was bright and smooth. Because of different glaze shrinkage rates, cracks of different sizes were formed with distinctive shapes. It excelled in glaze color, had no decoration, and represented ceramics of the Northern Song Dynasty and the Southern Song Dynasty Celadon from the Longquan kiln(in today’ s Longquan, Zhejiang ) excelled in carved and impressed patterns and was later famous for the luxuriantly green glaze color
Tea fight was popular in the Song Dynasty. black-glaze tea cups were favored for a hile because they could set off white tea foam and facilitate tea color observation, and tea utensils thus had cultural value in addition to the thirst-quenching function Among them, rabbit hair cups from the Jianzhou kiln in Fujian(in today’s Jianyang, Fujian) had crystalized rabbit-hair-shaped or oil-drop-shaped spots throughout blackglaze; colorful sparks around big crystalized spots in changeable-color cups were as wonderful as the solar halo. black porcelain from the Jizhou kiln in Jiangxi (in today’s Jian, Jiangxi) also had great originality. Oil drop, hawksbill and partridge spots formed by iron in glaze were used as decorative patterns, and leaves and paper cutouts were used as decorations-after treatment, leaves were affixed to cups and burnt, giving them natural beauty; decorative paper cutouts with both patterns and words were affixed to semi-finished products before application of glaze, making them look simple and festive
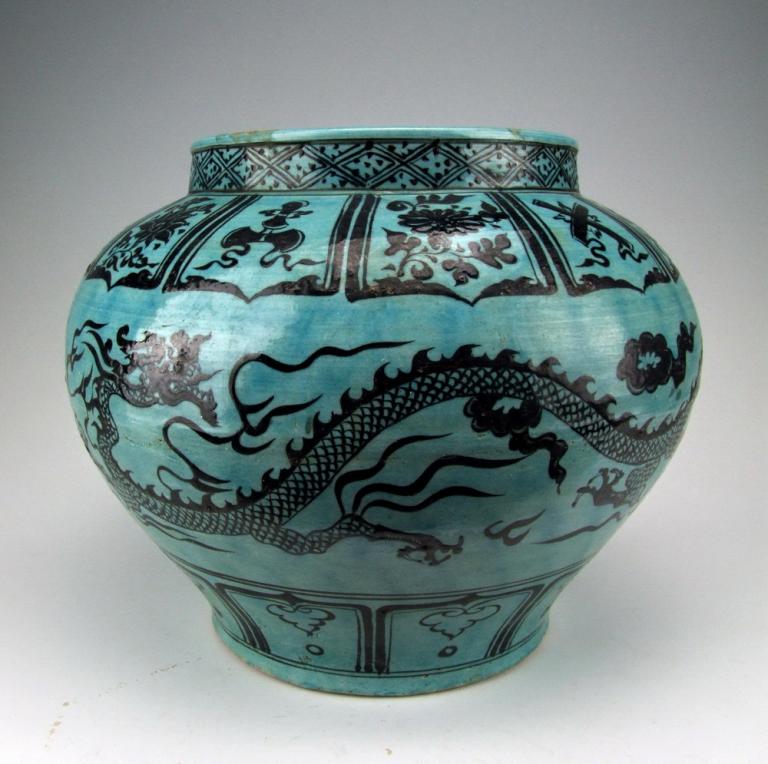
Celadon Cong-type bottle, 19.7cm in height, made by an imperial kiln in the Song Dynasty, kept in theTokyo National Museum. People in the Song Dynasty were fond of the antiques and modeling the antiques This bottle was modeled after the Cong
Crimson purple glazed crabapple-shaped flowerpot, 14.4cm in height, made by Jun Kiln in the Song Dynasty, kept in the National Museum of China. The monotony of the monochrome glaze is broken through transmutation. It is sky blue at the inner side of the flowerpot and crimson purple at the outer side. This flowerpot is used together with the matched support
The Yuan, Ming and Qing dynasties were a new stage of Chinese ceramic production techniques’ development Color-painted porcelain with many shapes, dazzling glaze colors and splendid decorations was quite popular. Color-painted porcelain can be classified into underglaze porcelain and overglaze porcelain Underglaze porcelain was covered with a layer of transparent glaze after the semi finished product was painted with colors and burnt at high temperature in one go. It was characterized by mild, smooth, light and elegant colors, and meanwhile colors did not wear out or change easily under glaze. However, because underglaze pigments nust be burned at high temperature and there were not many pigments capable of withstanding high temperature its types were far less abundant than those of overglaze porcelain Burnt porcelain ware was painted with colors and then baked in the kiln to produce overglaze porcelain Because baking temperatures were not high and there were many pigments capable of withstanding such temperatures, it had abundant colors. However, because decorations were over glaze, they wore out and changed color easily after friction or contact with acid or alkali.
Blue-and-white eight-prismatic Yuhu Chunping with a pattern of playing lion made in the Yuan Dynasty, 325cm in height, kept in Hebei Provincial Museum. The Yuhu Chunping of the Yuan Dynasty has 9 decorative layers as the Mongol nationality regards the number 9 as significant. The eight-prismatic shape makes it easy to hold the bottle, which is applicable to the migratory life Porcelain capital Jingdezhen rose in the Yuan Dynasty, and blue and white
porcelain and underglaze red porcelain were the most typical types. At that time, the only government-run kiln-the Fuliang porcelain factory-was also located here. blue and white porcelain was underglaze color-painted porcelain with cobalt oxide as color retention agent, having blue patterns against white backgrounds or white patterns against blue backgrounds. It was burnt at high temperature in one go after being glazed, the working procedure was simple, and its application was extensive. Because of different shades and layers of color blue and white porcelain ‘s artistic effect was simple and elegant, rich and unified, and liked by many people. After the Yuan Dynasty it became the main type of chinese ceramics most decoration themes were traditional ink and wash paintings, clear, elegant and extremely charming. Influenced by dramas and novels themes also included historical figures novels and legends the sudden rise of blue and white porcelain in the yuan dynasty should have to do with Mongolians’ fashionable colors of blue and white and their customs in the yuan Dynasty, many artworks’ backgrounds were blue and white, and mongolians liked nine and detested seven, so blue and white porcelain mostly had nine layers of decorationsinstead of seven layers. They ate and drank without restraint, roved around as nomadsand usually had large portable utensils. blue and white porcelain was also influenced by the Islamic culture. Cobalt came from the West, the composition mode of multiple decoration layers surrounding utensils was similar to Western asian metal utensils and even their main collectors were also in islamic countries because white was fashionable, egg-white glazed porcelain produced in Jingdezhen was also popular in the yuan Dynasty
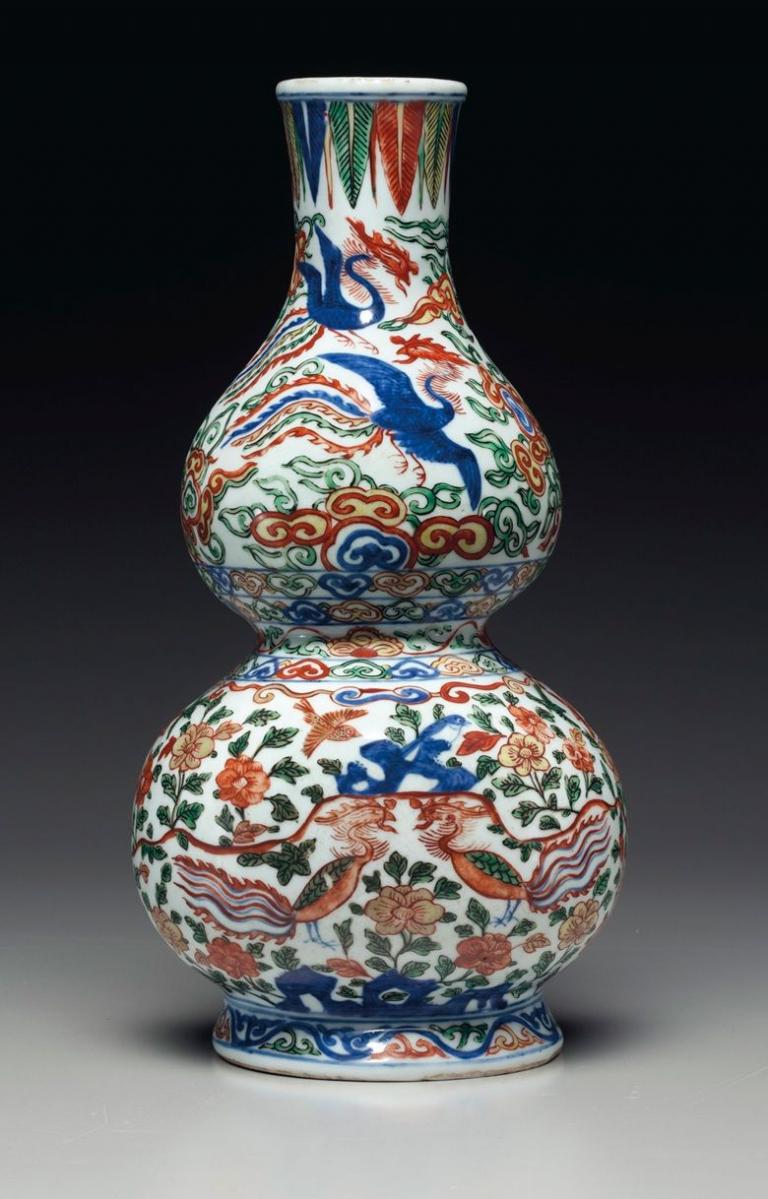
Blue-and-white flat bottle with sea wave dragon pattern of the period of the reign of Ming Emperor Xuande, 46cm in height, kept in the National Museum of China. The bottle was fired in the Imperial Ware Factory in Jingdezhen with”Suboniqing being used as the cobalt paint to form the blue and white dragon pattern. With an elegant style, the bottle has fine and smooth base and bright and glossy glaze with bright colors and vivid pattern
Underglaze red porcelain was named after its red underglaze. It was at first a naturally formed colored glaze effect, and later became a type of artificial decorations Underglaze red porcelain with splendid colors and a lively atmosphere conformed toChinese traditional habits, and was widely welcomed after its burning began in the Yuan Dynasty. Underglaze red porcelain was generally called “blue and white porcelain with purple decorations, “i.e. decorating blue and white porcelain ‘s patterns with fruit, pistils, etc. drawn with bronze red and was famous for dazzling colors. Because it wasvery difficult to burn it successfully, patterns were usually blackish brown, and most exquisite products came from government-run kilns in the Ming and Qing dynasties
Shi Dabin-style boccaro loop-handled teapot of the Ming Dynasty, 20.5cm in height, kept in Nanjing Museum. As a masterpiece, the teapot is elegant, plain but delicately beautiful
In the Ming Dynasty, new breakthroughs were made in porcelain production techniques. Pottery wheels for rotating semi-finished products replaced bamboos and knives, and glazing by blowing replaced glazing by immersion, greatly improving porcelain quality and output With economic and transportation development, a lot of porcelain was burnt in government-run kilns and private kilns in the Ming Dynasty to meet the demand for porcelain for the imperial court’s enjoyment, ordinary people’s daily use and foreign trade. Ming porcelain was famous for colored painting and colored glaze, and products of the Jingdezhen imperial utensil factory that specially burnt ceramics for the imperial court were most representative in the Xuande period(1426-1435), smalt”imported from Southeast Asia was used as blue and white porcelains raw material, and sedate and elegant porcelain with different shades ofcolor was most famous Contrasting colors emerged in the Xuande Period, and thrived in the Chenghua Period(1465-1487).Underglaze blue and white patterns were burnt,overglaze colored paintings were baked,and the upper and lower layers combined into a complete pattern.Such porcelain was refreshing,elegant and reputed.After the Jiajing Period(1522-1566),five-colored porcelain thrived.There were two types of five-colored porcelain:five-color blue and white porcelain”formed by underglaze blue and white patterns and overglaze colors and overglaze five-color porcelain formed by overglaze colors alone both were baked twice with bright colors画
Famille-rose square brush pot with landscape pattern,19.2cm in height,made by Wang Yeting(one of the members of the”Eight Friends of Zhushan”)in Jingdezhen,Jiangxi in 1932.The four sides of the body are decorated with traditional landscapes and poetry calligraphy with spot-ink and light ink stroke skills,creating rich layers
In the Ming Dynasty,there were numerous types of single-color glaze such as shiny red glaze in the xuande period with a solemn dark red tone and tender yellow glaze in the Hongzhi Period(1488-1505)and the Zhengde Period(1506-1521),which was crystal-clear,even and pure with the exclusive imperial color and also used on products for the imperial court only Jingdezhen was still the national porcelain production center,and celadon from Longquan,Zhejiang white porcelain from Dehua Fujian,purple sand pottery from Yixing,Jiangsu,etc were also famous both at home and abroad.among them white porcelain buddhist statues from dehua were most peculiar.He Chaozong(1522-1600)was an expert in this area.Purple sand pottery was named after the purplish red color of purple sand clay with excellent shapes.the onger they are used the mellower tea tastes.Gong Chun and Shi dabin(1573-1648)Underglaze polychrome long-neck bottle with a pattern of hyacinth beans and a couple of chickens, a representative work of the early underglaze polychrome porcelains made by Liling Kiln in Hunan in the early period of the former Republic of China, kept in Hunan Provincial Institute of Ceramics. The pattern is drawn through the technique of underglaze polychrome outline drawing color filling, creating rich colors and integrating the pattern with the body
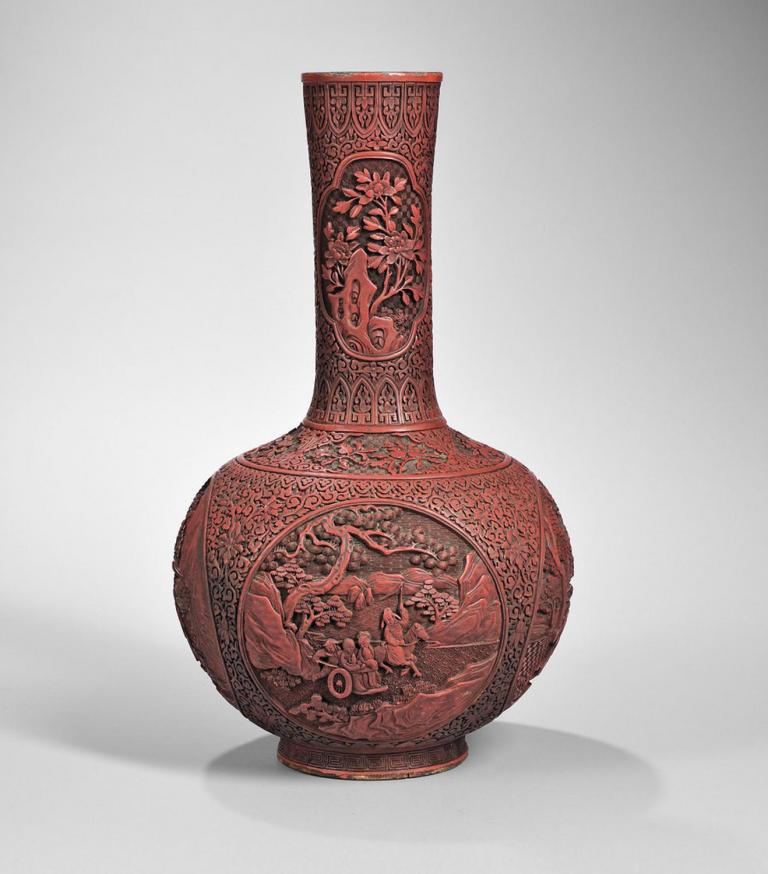
In the Qing Dynasty, color-glazed and color-painted porcelain were sti mainstream porcelain products represented by those made in the Jingdezhen imperialutensil factory, and peaked in the Kangxi Period (1662-1722), the Yongzheng Period(1723-1735) and the Qianlong Period (1736-1795). In terms of glaze colors, there were more types with dazzling colors-for example, there was cowpea red glaze in the Kangxi Period, jade glaze and rouge glaze in the Yongzheng Period, and glaze of many colors including red, blue, green, yellow and purple in the Qianlong Period. In terms of colored painting, ancient colors were called”hard colors”in the Kangxi Period. The five-color technique of the Ming Dynasty was inherited, blue overglaze was invented, themes were diversified, colors were bright, and layers were clear. Powder glaze, also called”soft color glaze,”was invented in the Kangxi Period, and thrived in the Yongzheng and Qianlong periods. Pigments were mixed with oil, and the method of washing with watercolors was adopted to enhance three-dimensionality. Tones were soft, and patterns exquisite. The quality of the imperial utensil factory’s products was the best, and private kilns also produced lots of products. Colored enamel porcelair was inspired by enamel paintings on bronze bases. The imperial court’s painters drew patterns on semi-finished products produced in Jingdezhen, and then they were burnt again. Their number was very small, and their grade was the highest. With sparkling colors, solid textures and exquisite patterns, they were also called “enamel paintings on porcelain bases. Colored enamel porcelain invented in the late Kangxi Period and made with imported enamel materials was also called “foreign procelain”; in the Yongzheng Dynasty, its raw materials could be acquired through burning in China, and in the Qianlong Period, its production reached a peak.
Polychrome vase with a pattern of flowers and birds of the period of the reign of Qing Emperor Kangxi, 455cm in height, kept in the Palace Museum in Beijing. As the shape of the vase is like the tail of the phoenix,it is also called “phoenix-tail vase. The pattern is delicately drawn through a realistic approach with bright colors, creating vivid image
Apart from the burning center Jingdezhen, ceramics were produced almost all over the country in the Qing Dynasty White porcelain from Dehua, Fujian, celadon from Longquan, Zhejiang, purple sand pottery from Yixing, Jiangsu and pottery sculptures from Shiwan, Guangdong all had local characteristics. Products were notonly supplied to meet demand from the imperial court and the public, but also sold in large numbers to countries around the world, especially European countries. Guangzhou was an important place of pattern processing for porcelain to beexported. Semi-finished white porcelain products made in Jingdezhen were glazed with colors and golden patterns. Elaborate-style painting and Western painting skills were also drawn on to create bright colors and sharp contrasts. Such products were called “Guangdong colored porcelain. However, after the Qianlong Period, Chinese ceramics declined gradually, and ceramic exports also dropped increasingly due to the rise of European porcelain production countries.
In the late Qing Dynasty and the Republic of China Period, ceramic art failed to reverse the overall declining trend in China’s domestic trouble and foreign invasion, though efforts were made to restore traditions, create new products and carry out international exchange and achieved results. In particular, colored ceramic painting progressed lot. After the late Qing Dynasty, to seek survival and development, anumber of painters went to Jingdezhen, engaged in colored painting on porcelain, and developed traditional overglaze decoration. In 1928, the first Chinese school of ceramic art “Eight Friends of Zhushan”introduced literati painting skills and aesthetic views into ceramic art circles, organically integrated traditional Chinese ink and wash paintings, artistic conceptions of and poems on them with color-painted ceramics, and made painted ceramics popular. At that time, ceramic sculptures were represented by color-painted ceramic sculptures suitable to both refined and popular tastes from Jingdezhen, traditional-style porcelain sculptures from Dehua, Fujian and pleasant and practical ceramic buildings, figure statues, utensils, etc. from Shiwan, Guangdong.
Boccaro pot with shape of monk”scap,hand -made- by Gu Jingzhou in197os. The Yixing boccaro pot with a shape of a monk’s cap was initially created by Shi Dabin. With a combined shape of square and round, its craft is complicated and elaborate and it is formed by joining 25 pieces of clays
Blue-and-White Porcelain Western Cutlery produced by Jianguo Porcelain Factory. In 1950, in light of the needs of national celebrations, Guo Moruo then Vice Premier of the Government Administration Council and Director of the Central Education Commission, proposed the establishment of a Design Council for “Jianguo Porcelain.
A Buddhism Goddess Guanyin Across a Sea, a white porcelain sculpture in Dehua Fujian made by Xu Xingtai in 1932. Guanyin is the traditional theme of the white porcelains in Dehua. The Guanyin has various styles and smooth lines of the clothes with much romantic charm.
In the early 20century, Xiong Xiling and others actively promoted the principlesof”establishing schools and setting up companies,” brought in talents, improved techniques, successfully produced underglaze pigments in Liling, Hunan, and created “five-color underglaze porcelain. The unfading white porcelain with smooth glaze and abundant colors won prizes at the Nanyang Industrial Exposition, the Turin Expo in Italy and the Panama Exposition in the United States. However, in 1931, the Hunan porcelain company went bankrupt, and production of Liling porcelain stopped.
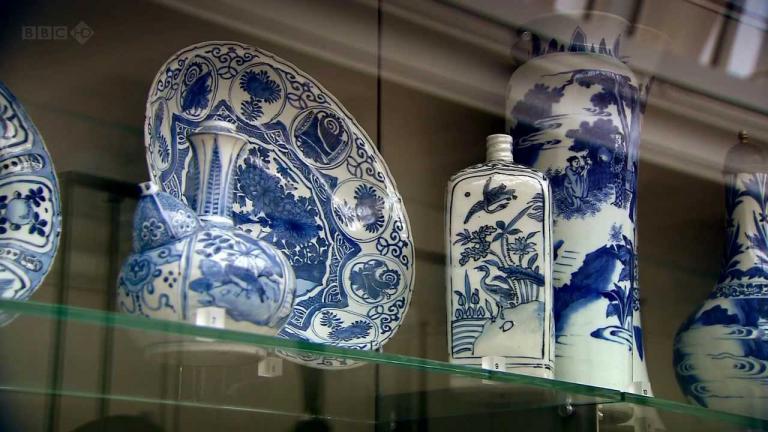
In the Republic of China Period, porcelain production techniques such as coal pit kiln design and burning, new mineral selection and pulverization methods, mud screening, shaping and glazing by blowing with machines, use of gypsum molds and shaping through grouting were introduced and experimented on a small scale. For example, purple sand pots from Yixing extensively praised since the Ming and Qing dynasties were usually shaped through beating mud strips and then inlaying them. Evenly thick pot bases were carefully made, and most pot bottoms had redial shapes. Before the mid-Qing Dynasty, all such pots were made manually; in the late Qing Dynasty, the technique of shaping with molds or winches emerged; in the modern period, some were shaped through grouting. At that time, sand was as thin as plaster, pot bodies became quite shiny after being modified slightly, and utensils were regular and smooth both inside and outside. A lot of skillful craftsmen good at producing purple sand pottery emerged in Yixing, but in the early195os, due to the chaos caused by war, there were only more than 50 people engaging in purple sand pottery production and more than 20 craftsmen able to produce pots in Yixing.
After the People’s Republic of China was founded in 1949, the government carried out the work of “protecting, developing and improving”arts and crafts, and the ceramic industry revived. Traditional craftsmen were brought together again to teach apprentices; ceramic research institutes, specialized ceramic schools (e.g. the Jingdezhen Ceramic Institute established in 1958 and ceramic schools at all levels in major porcelain production areas), and ceramic departments of higher fine arts schools (e.g. the Central Academy of Craft Art established in 1956 set up the ceramic department earliest) were set up successively to systematically foster talents; famous ancient kilns’ traditional techniques were restored, and engineering and technology experts used scientific methods and testing means to carry out experimental analysis and theoretical summary; traditional ceramic techniques were restored, and the time spirit was integrated into ceramic art Artistic porcelain with a strong atmosphere of real life and the times and economic and unadorned everyday porcelain became two mainstream types then. China’s modern ceramic industry was concentrated in the following production areas: Jingdezhen in Jiangxi, Liling and Tongguan in Hunan, Fengxi and Chaozhou in Guangdong, Yixing in Jiangsu, Dehua in Fujian, Yuzhou in Henan, Zibo in Shandong, and Tangshan and Handan in Hebei.
Folk ceramic burning kilns are widely distributed. Because reserves of raw materials for burning pottery abound in various places modern folk ceramics are mainly pottery ware made using local materials, having unadorned shapes, unique functions, excellent quality, reasonable prices and prominent regional and ethnic features. Black pottery and grey pottery from Xishuangbanna, Yunnan are most peculiar. Dai people and Wa people still use ancient pottery production methods and burn pottery outdoors, and their pottery has simple styles and practical shapes; there are numerous roof-ridge animals of divers shapes in Dali and Kunming. Products from folk pottery kilns around large cities meet specific needs in modern life with unique functions and decorative shapes-for example, water pots and sand pots from Tongguan, Hunan, blessing jars from Hanchuan, Hubei, black glaze pots from Huating, Gansu, pickle jars from Rongchang, Sichuan, and purple pottery steamer pots from Jianshui, Yunnan. Besides, traditional purple sand pots and garden glaze porcelain also got a new lease of life thanks to the popularization of tea culture and garden art; the method of producing rough pottery carefully improved kitchen utensils, lights, pottery tourist goods, pottery sculpture toys, pottery furnishings etc., and expanded the use of pottery ware.
Traditional pottery art focuses on practicality and decoration, brings raw materials’ special qualities into full play, gives emphasis to the beauty of craftsmanship, and contains abundant cultural connotations; modern pottery art takes pottery clay and porcelain clay as materials, expresses new artistic concepts and aesthetic views without limiting itself to traditional rules on ceramic production, and emphasizes experimental exploration of mud and glaze. In the early 1980s, China mainland’s modern pottery art first received attention from higher art schools’teachers and students. They went to ceramic production areas for practice, and attracted many artists to participate. After 1997, a series of modern pottery art exhibitions and education seminars were held. Pottery artists actively participated in Chinese and international modern art creation, focused on the expressiveness and experimentation of art, gave attention to the issue of human existence on the basis of individual experience, and were more concerned about the relationship between individuals’ destinies and their surrounding living and social environments. Modern pottery art’s emphasis on daily life is also a return to Chinese traditional ceramic culture in a certain sense.
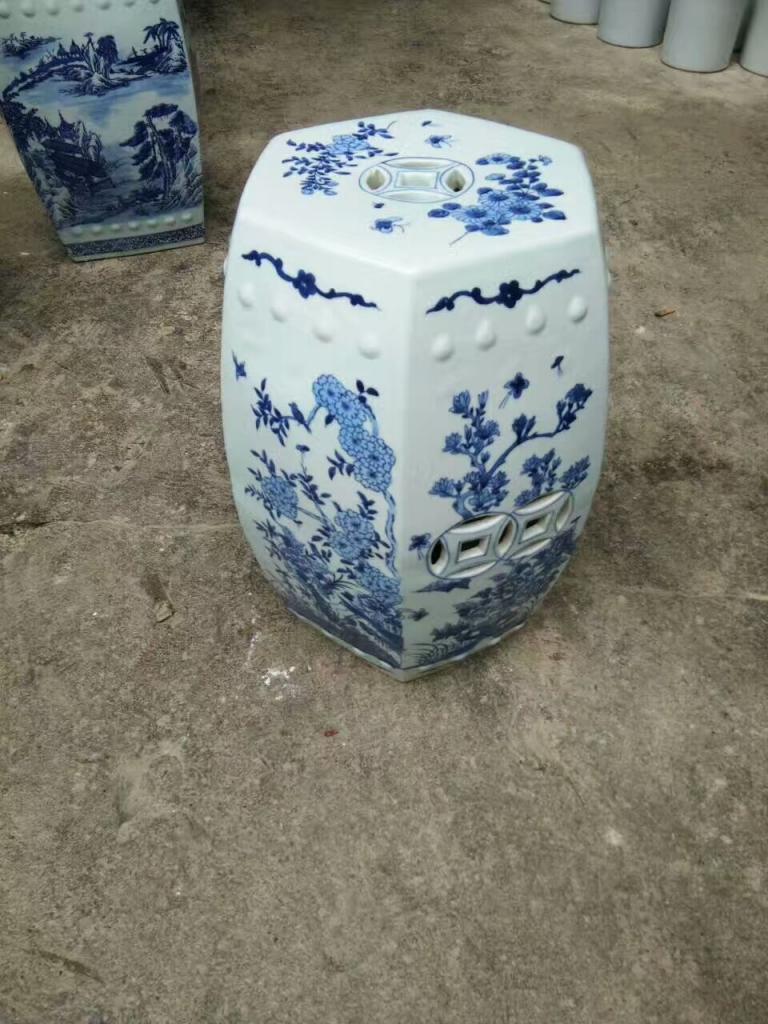