Enamelware in China
8 min readEnamel was also calledfo-fo-lin,””fo-lang,”fu-lang”and”fa-lanin ancient China. The making of enamelware is actually a composite craftsmanship of enamel craft and metalwork. First, quartz, porcelain clay, feldspar, borax and metallic minerals were smashed and made into enamel powder, and then, smelt them in the furnace, paint them on metallic base, and finally, roast the enamelware in the furnace and make it cool down. Some enamelware needs to be polished and gold-plated. Enamelware not only has the robustness of metal, but also the smoothness and corrosion resistance nature of glass. It has both practicality and aesthetic beauty.Filigree enamel elephant-ear furnace of the Yuan Dynasty, 13.9cm in height, kept in the Palace Museum.The furnace is made up of copolymer copper and plated with gold and it glazing color is darker, showing eleganceFiligree enamel Yuhuchun Vase of the Ming Dynasty, 27.1cm in height, kept in the Palace Museum.
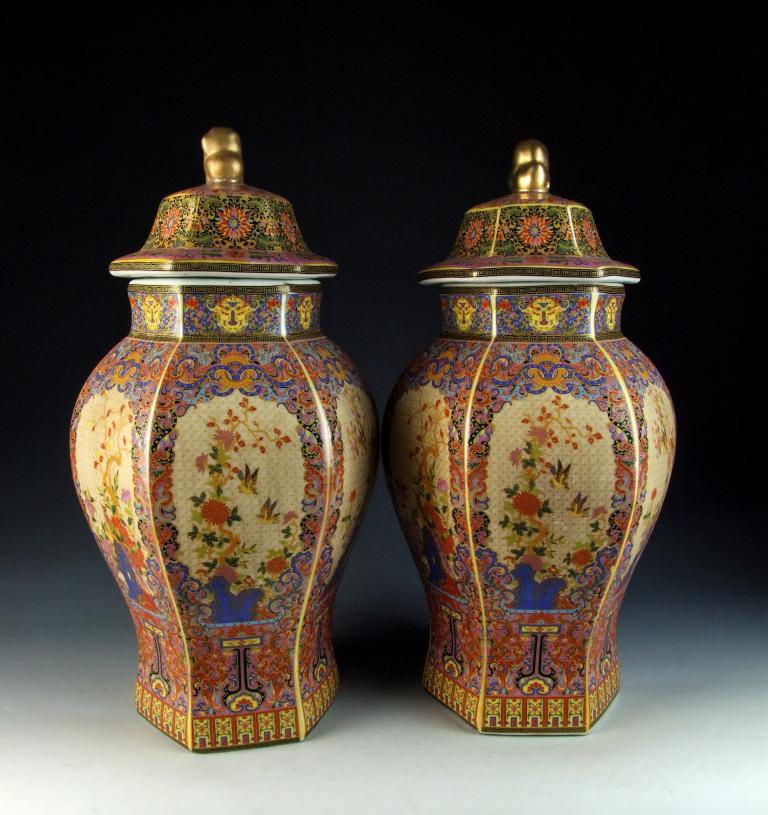
Manufactured by Imperial Workshop in the Ming Dynasty, the vase is made up of copolymer copper and plated with gold, with flat and smooth surface and gorgeous glazing color. Phoenix-design double ears and mouth in the shoulder part and its feet are added in the Qing Dynasty. China started to make enamelware later than other countries. As we know, the earliest enamelware produced in China is the “silver-base gold cloisonne enamel mirror of Tang Dynasty, “which is kept in Shoso-in in Japan. However, no other enamelware was made in China in the three to four hundred years later. The origin of enamelware in China remains to be confirmed after the excavation of new enamelware of Tang Dynasty, Five Dynasties and Song Dynasty. The existing real objects and literature showed that Yuan Dynasty is an era that enamel craft came into being and grew mature in China. A collection of enamelware of late Yuan Dynasty could be found in the Palace Museum. For example, the body of a beast-ear tricyclic vessel is made of a cloisonne enamel jar of late Yuan Dynasty. It has the typical broad shoulder and narrow abdomen in enamelware of Yuan Dynasty. It is decorated with patterns of cloud, leaves and lotus flowers. The enamel has delicate texture, vivid colors and smooth surface, which is similar to the enamelware being made in Constantinople from the 10n to 12 century.
This batch of enamelware of late Yuan Dynasty is the first generation of copper-base cloisonne enamelware in China. It is no longer affected by Arabian culture and has more Chinese features.Painted enamel Chinese-flowering-crabapple-design furnace of the Qing Dynasty, 50.5cm in height, kept in the Palace Museum. Manufactured in Guangzhou, it is made up of copolymer copper and plated with gold Its body, mouth and feet are all in a form of begonia flower. Based on traditional Chinese style, it absorbs western mental finishing and highlights the color of gold, presenting a luxury and magnificent look. Enamelware could be divided into several types based on production methods, such as cloisonneenamelware, chisel-based enamelware (champleve)and painted enamelware. It could also be divided into several types based on the type of base, such as gold-base enamelware, copper-base enamelware, porcelain-base enamelware, glass-base enamelware and purple sands-base enamelware. The copper-base enamelware is the most popular one because copper will easily combine with the enamel on the surface and the price of copper is more acceptable than other materials. The scientific name of “Jing-Tai-Lan cloisonne, a renowned traditional craft of China, is “copper-base cloisonne enamel” This kind of enamelware was popular in Ming Dynasty under the reign of Emperor Jingtai (1450-1456). Its name was “Jing-Tai -Lan,”because it was exquisitely made and the glaze was blue. The processes of making “Jing-Tai-Lan” cloisonneinclude base-making cloisonne, welding, blue-filling, blue -burning, polishing and gilding. In the process of blue-filling, the craftsman would use a small iron spade (also called “blue gun”)or a glass tube to fill glazes of various colors into the profile of patterns. The ground color would be added first, and the flowers would be added later. Finally fill in the blue color and the bright white color. The process of blue-filling and blue-burning would be repeated for several times. A blue-filling process would be followed by blue-burning process.
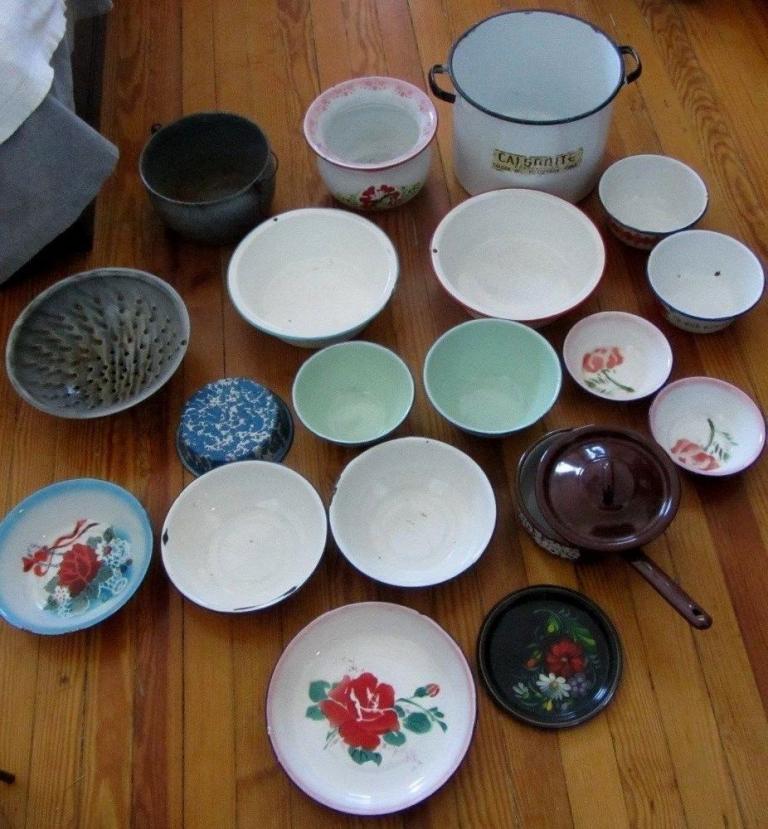
These processes would be repeated for over three times for making each piece of exquisite cloisonne enamelware. ① Painted enamel landscape-design furnace of the Qing Dynasty, 5.4cm in height, kept in the Palace Museum. Manufactured by the palace workshop of the Hall of Mental Civilization, it is made up of copolymer copper and plated with gold. The furnace is fully based on light yellow glaze, with landscape design painted with light blue glaze. ② Filigree enamel oil warmer of the Qing Dynasty, 16.2cm in height, kept in the Palace Museum. Manufactured by the palace workshop of the Hall of Mental Civilization, it is made up of copolymer copper and plated with gold, with brilliantly shinning enamel. There are three copper rings in different sizes inside the ball. Such three rings encircle each other with the same core and are well structured, keeping the furnace core horizontal.③ Painted enamel lotus-design pouch-shaped snuff bottle of the Qing Dynasty, 3.5cm in height, kept in the Palace Museum. Manufactured by the palace workshop of the Hall of Mental Civilization, it is made up of copolymer copper and plated with gold. It is in a form of flat pouch, with a square shoulder. Based on white glaze, its two sides are designed with lotus. The royal blue glass cover is connected with ivory spoon. In early Ming Dynasty, Cao Zhao explained the origin, features and application of enamel craft for the first time in his book, “Essentials of Identifying Antiques, “which is the earliest monograph of China on the identification of cultural relics. It is also the only literature for modern people to study enamelware of ancient China. Enamelware of Ming Dynasty has two categories. Most of them are cloisonne enamelware. Chisel -based enamelware was rarely seen nowadays. Mr. Yang Boda’s researches showed that the developing process of cloisonne enamelware in Ming Dynasty could be divided into four phases: 1) Phase of Emperor Hongwu and Emperor Yongle: So far, no enamelware with chronological records has been found. 2) Phase of Emperor Xuande, Emperor Jingtai and later: The enamelware in this phase has vivid cloisonne, stringent composition of picture and elegant atmosphere. 3)Phase of Emperor Jiajing: The enamelware in this phase has compact composition of picture, bold and unconstrained cloisonne and striking contrast of colors. 4) Phase of Emperor Wanli and later: The enamelware in this phase has complicated composition of picture, rough cloisonne, enthusiastic hue and changing style. Currently, only cloisonne enamelware being made under the reign of Emperor Xuande, Emperor Jingtai, Emperor Jiajing and Emperor Wanli has memorial patterns. Enamelware made under the reign of Emperor Xuande is the most exquisite one. Under the reign of Emperor Xuande of Ming Dynasty, in an ancient Chinese book written by Wang Zuo, it said that “enamelware the utensil used by women in the bedroom, not the utensil for scholar-officials to use in the study. “At that time, enamelware was not an elegant utensil in the scholar-official’s heart, but women like it, and the imperial court attached great importance to it. To satisfy the needs of the imperial court, wire-inlaid enamelware was made in special workshops employed by the emperor. We can still see the enamelware being made at that time, such as furnaces, cups, bottles, boxes, wine vessels, candle holders and spindle heads.
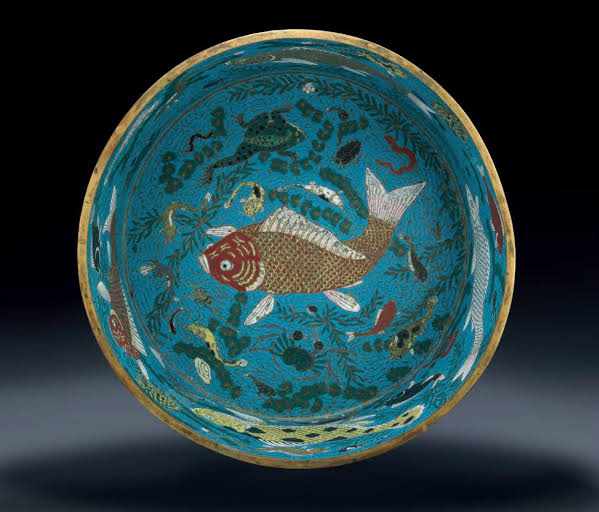
The existing largest and most delicate enamelware of Ming Dynasty is the “wire-inlaid enamelware jar being made under the reign of Emperor Xuande.” It was made in special workshop of the imperial court and is now kept by British Museum in UK. Eight-piece food box was designed and manufacture by Qian Meihua in 1975. Due to the great advocate and support of the imperial court, the enamelware processing crafts developed rapidly based on the techniques of Ming Dynasty and Yuan Dynasty. Under the reign of Emperor Kangxi, cloisonne enamelware factory was established in the imperial court for making cloisonne enamelware and chisel -based enamelware. Later, the factory also succeeded in making painted enamelware. Painted enamelware has exquisite shape and rich glazing color. It is similar to pastels on the early stage. Porcelain-bodied enamelware(enamel painted porcelain) is the painted enamel on porcelain body. It is a perfect combination of the porcelain and the painted porcelain craft. Under the reign of Emperor Qianlong, painted enamel craft was highly prosperous in China. Most painted enamelware was produced in the imperial court, Guangzhou and Yangzhou. The painted enamelware produced by the imperial court has neat patterns, exquisite drawing skills and elegant flavor. Most enamelware has bright yellow color and distinctive royal atmosphere. The painted enamelware in Guangzhou has broad lines and complicated composition of picture. Most enamelware was decorated with European-style rolling leaves, and was painted with enamel glaze imported from western countries.
The glaze has vivid colors and bright gloss. At that time, snuff bottles made of enamel, jade, crystal, agate and porcelain appeared in China. They were made with exquisite painting and calligraphy arts and have diversified shapes. The paintings on these snuff bottles have diversified styles and were rarely seen in dynasties in the past, such as western women, babies and western-style pavilions. Most cloisonne enamelware in Ming Dynasty and Qing Dynasty was used by the royal family in the imperial palace.
In general, its shapes, decorations, colors and craftsmanship were complicated and luxurious It was not until in late Qing Dynasty that common people were allowed to make and use cloisonne enamelware. At that time, there were several privately-owned workshops for making cloisonne enamelware such as Lao-Tian-Li, De-Xing-Cheng, Jing-Yuan-Tang and Zhi-Yuan-Tang. Cloisonne enamelware made by these workshops has three grades: 1) High-grade antique cloisonne enamelware for export: For example,the”Baoding Cauldron” made by Lao -Tian-Li won a First Prize on Expo Chicago in 1904. It won First Prize again on Panama World Expo in 1915. Since then, cloisonne enamelware became a world -renowned handicraft, and a large quantity of cloisonne enamelware was exported to foreign countries. 2) High-grade display articles, such as the five sacrificial utensils and mirror screens. 3) Cheap cloisonne enamelware, such as smoking sets, jewelry boxes and items for daily use. The social instability in modern China resulted in a decline of cloisonne enamelware-making industry in Beijing. In the period of the Republic of China, all cloisonne enamelware was made by privately-ow workshops. At that time, the cost of making cloisonne enamelware was nearly twice as the cost of making copperware. The number of process also decreased from over 40 to 20. Most cloisonne enamelware was article for daily use. It was no longer exclusively used by the aristocracy, but ordinary people. Most cloisonne enamelware was roughly made. After 1949, Cloisonne was an artwork exported for a long time, and the antique reproduction continues to be produced till now. As more and more professionals engage in the industry, features of traditional Cloisonne such as modest shape, wide varieties, full pattern, vivid color and elaborate wire work are retained, traditional products are reproduced and new products for decoration or utility purpose are developed. For example, in 1950-1951, a group consisting of Mo Zongjiang, Chang Shana, Qian Yuehua, Sun Junlian, etc., under the leadership of Lin Weiyin, an architect from Civil Engineering of Tsinghua University conducted a survey on the conditions of Cloisonneworkshops in Beijing, and later designed a new pattern for Cloisonne with national style and time feature for Beijing Special Arts and Crafts Company.
In 1959, designers and craftpeople created a Cloisonne Goldfish, Lotus and Large Fish Tank for the Great Hall of the People, which has novel shape, vivid pattern and plain features. The Cloisonne products produced before 1966 are various in kinds, novel in shape and delicate in polishing, exported to more than 90 countries. High-class Cloisonne products are presented as a national gift to other countries. Middle-class gifts, such as vase, lamp, pocket watch, pen, are also widely presented.
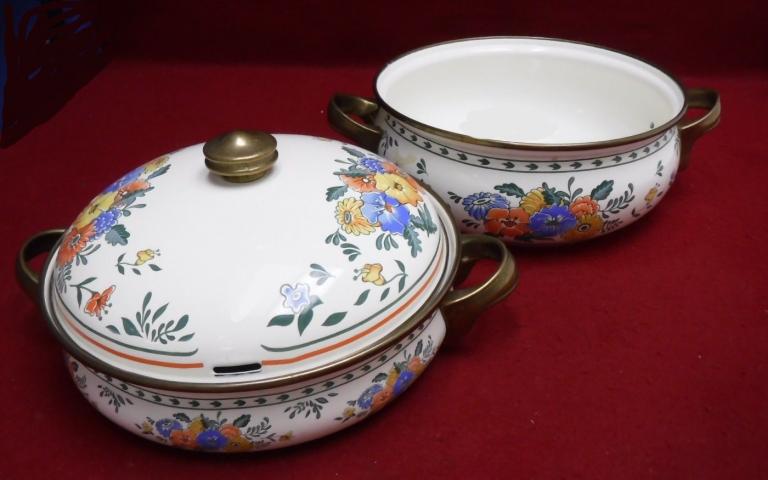