Tackle the Heavily Weathered Soil Layer and Permeable Sand Layer
11 min readIn December 2005, the weather turned cool in Xiamen. In a small village named Gaolin in the easternmost part of Xiamen Island, the chilly wind was blowing from the sea, but in the nearby construction site of Xiangan Tunnel, the original ponds and farming fields were bustling. Various machinery and equipment were creating a real atmosphere on the site.
“We were working to overcome the first hurdle.”Wang Xuebin, Project Manager of the Wutong end of Xiangan Tunnel, said. He was standing beside the muddy tunnel entrance in overalls, boots and helmet. The workers beside him were putting the steel pipes into the fracture surface of the soil layer. The steel pipes were laid in a circumferential direction with specific spacing, forming the steel pipe-shed support, also known as”pipe roof”.
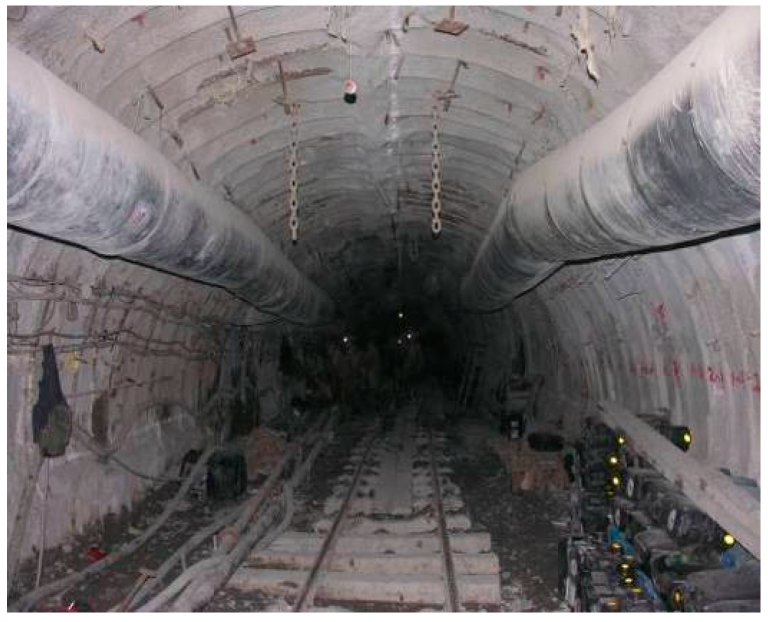
The technical problem at the starting point of Xiang’ an Tunnel construction was the heavily weathered soil layer. The length of the onshore shallow buried section on the Xiamen side was 6,244 m. The shallow buried section with a burial depth of 5-17 m acz`counts for over 80% of the total length of the onshore shallow buried section. It was composed of heavily weathered granite. It was the V-level surrounding rock, which would make the tunnel shallower.
It was a great challenge to excavate a large three-lane tunnel with a span of 17.5 m in the V-level surrounding rock which was soft soil similar to the mud. In contrast,a single-hole two-lane tunnel was more common. However, taking into account its specific needs, Xiangan Tunnel was designed to be a single-hole three-lane tunnel. Compared to the two-lane tunnel, the three-lane tunnel was near impossible, as their ability to withstand pressure was quite different.
How do you excavate such a huge tunnel and keep it from collapsing? If the whole tunnel was excavated at once, it would collapse easily, and even an entrance could not be excavated out.Meanwhile, the soil layer pressure caused by having a large cross-section would be different. If the steel stent was used for support, with the pressure of the heavy weathered layer, the two-lane tunnel might only settle 20 cm, but a three-lane tunnel would settle 50-60cm.
Therefore, the workers had to put the steel pipes into the soil to form a pipe roof, just like burying the “bones”into the soil. The workers would then press the cement paste into the surrounding rock fractures through the pipe wall for the cementation and consolidation of the loose soil. After this, the tunnel would not collapse when the soil below the pipe roof was excavated out.
In addition to the strong support from the pipe roof, the CRD method and the double side drift method were also adopted during tunneling.
In the CRD method, the large section tunnel would be divided into four relatively independent caverns for construction, following the construction principle of “small segments, short steps, short cycling, quick closure, frequent measurements, and strong support”. The construction would be conducted from the top to the bottom, forming the ring segment by segment and supporting while tunneling, in order to achieve better support.
The construction scene adopting the CRD method should be like this: in a circular tunnel,a large section is divided into four small caverns, with workers working in each cavern. It looks like a part of the “honeycomb”. Especially under the light, this scene is just like a “four-frame comic strip”.
The double side drift method can control the surface subsidence, and maintain the stability of the tunnel face, which is very safe and reliable. Its principle is two middle-walls which are used to divide the large section into three small sections for construction. The guide tunnels in the left section and the right section would be constructed first, and then the middle section would be constructed last. After the completion of the supporting inverted arch, the temporary support to the guide tunnels on both sides would be removed to form a whole section. The guide tunnels on both sides were shaped like an inverted oval, which would prevent vault crown settlement.
In these two approaches all of the large section was divided into several small sections, for excavation and support, which subtly decomposes the pressure from the soft soil.
“By using this method, the advancing speed of Xiang’ an Tunnel excavation would reach 1 m to 1.5 m per day, while in the similar soil conditions, the original speed should be only 1 m per day.Compared with other similar projects in China, this speed was quite fast.”Wang Xuebin introduced,”In order to accelerate the progress, we built two artificial islands on the shoals at the two ends of the tunnel, each with a diameter of about 100 m, and excavated a shaft to the main tunnel. One shaft would provide two more working faces, so the construction side would be able to excavate from both ends of the soil layer.”
Moreover, these two shafts would become ventilation shaft of the tunnel.
The shaft construction was very dificult. First,a vertical well should be excavated out by manual and mechanical forces. Since it was not a small-diameter well, the excavation was not easy.When it reached a certain depth, it would be difficult for the workers to get down, so a stairs must beconstructed on the wall of the well. As the shaft went deeper, it would be difficult for the machine to go in and for the muck to come out. But with the workers’ effort, the shaft extended bit by bit…
The working environment underground was very stifling. In the summer of 2006, the surface temperature of Xiamen reached 35 degrees Celsius. It was underground construction, and there wasonly the shaft for ventilation. Furthermore, the machine operation heat and the cement hydration heat increased the temperature in the shaft to about fifty degrees Celsius. Between about thirty and forty meters down the shaft, there was dripping water and mud on the wall. The clean clothes wouldbecome full of dirt in an instant, so the workers had to work shirtless, letting the sweat and mud flow over their bodies.
“We must overcome the hardships. If we do not increase the working faces, and only rely on the tunneling on both sides, we could not keep up the schedule.”Wang Xuebin said.
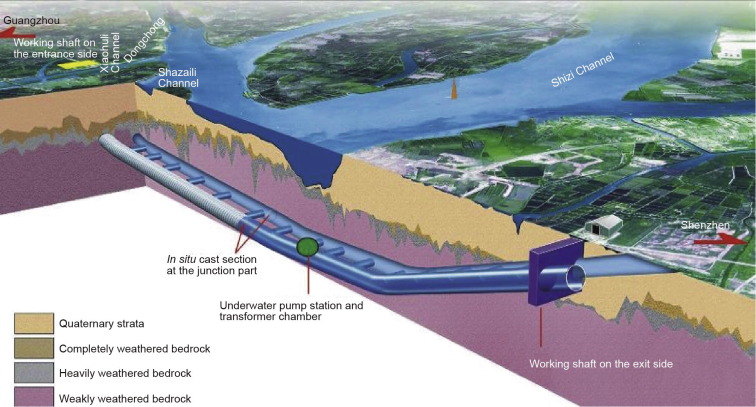
The undersea tunnels are normally excavated from both ends, so they has the characteristics of fewer working faces, long single head working distance, low efficiency, and long duration. With the addition of the three engineering difficulties of Xiangan Tunnel, the poor geological conditions, the complex construction process, the slow construction speed, and the broken bands in the undersea hard rock segment, the construction was more difficult than expected, which led to delayed progress. During the construction process, through the addition of incline shafts, vertical shafts, advance service channel and other measures, the investment in personnel and equipment, and the opening of new working faces(the largest number of excavation working faces at the same time was 14),a time duration to build a long tunnel was achieved, and the project schedule stayed on track.
The shaft construction was also accompanied by risks. In the evening of June 9,2006, when the shaft construction reached 15 m underground, it touched the surface of the sand layer. During the construction, the workers found that there was water gushing. They immediately took measures to block it, and planned to continue the work. After knowing the situation, Wu Chi, Deputy Manager of Xiang’ an Tunnel A4 Section Project Department of China Railway First Group Co., rushed to the site, asked them to stop the construction immediately, and to evacuate personnel from shafts. He stayed at the site, and withdrew all the large machinery and equipment before dawn.
His judgment was very right. At noon, the shaft was in danger again. This time the water and sand gushing momentum was much stronger than the first. The groundwater column spewed out with a lot of sediment. The depth of the silt in the shaft was increased by over 6m in less than 10 minutes.”Afterwards we all felt scared when we thought back. At the time, if the personnel andequipment were not evacuated in a timely manner, the consequences would be disastrous.”Wu Chi said.
Li Zhijun, Director of the Engineering Department of Xiamen Xiangan Tunnel Project Department of China Railway First Group Co., was also impressed by the rescue,”There were over20instances of rescue during the Xiang’ an Tunnel’s construction. That was the most impressive one.All the people there were shocked, because no one had ever seen such huge sand gushing. To be honest,I was very nervous. However, through this rescue, we had mastered the ‘ construction method of a large diameter shaft on the sand layer of the shoal.”
In addition to the technical difficulties, the construction on the two ends of the Xiangan Tunnel also had to overcome the impact of the weather. Xiamen is located in the southeast coastal area. It was the typhoon season from May to October, which caused many troubles during construction.
On May 18,2006, Typhoon Pearl attacked Xiamen. Since the flood control standard of the villages around Wutong Tunnel Entrance was too low, the drainage channel of the village breached in the early morning.
Suddenly, the rainwater converged into a river, running towards the low-lying Xiangan Tunnel, and constantly rushing the tunnel under construction. At that time, the construction was carried out in the soil layer section, so a dry environment was especially needed. The soaked tunnel face would easily collapse and cause the instability of the tunnel.
At this time, the emergency team immediately activated the emergency plan, evacuated the construction workers to a safe location, and mobilized hundreds of experienced workers to form a rescue team.
“Although it was a rescue, headquarters was very nervous. There were hundreds of people in the rescue team, and their lives and safety were the priority. It needed very calm judgment and command to ensure their safety during the rescue of the tunnel.”
With a perfect rescue plan, the orders were issued systematically. The priority was the water shutoff. Some rescue workers were in a relatively safe location. They were trying to block the water by construction machinery and sandbags. Meanwhile, some workers used various mechanical pumps on the site to drain the water, cleaned and reinforced the tunnel. After hours of fighting, the working faces of the tunnel were saved.
“This successful rescue made us realize that the perfect degree of the on-site plans and a variety of emergency supplies would directly determine the rescue efficiency and the success rate.”Zeng Chao said,”After the storm, the Project Department continued to strengthen the anti-flood and anti-typhoon measures surrounding the tunnel. In subsequent strong typhoons, there was no loss.”
At the other end of Xiangan Tunnel,which was Liuwudian side,Su Wende,the Project Manager of the Xiang’an side,also had a tough time.He met the problem of water-rich sand stratum.
The water-rich sand stratum on the shoal of the Xiangan side was over 600 meters long.After surveying,it was found that 205 m of it was on the right channel,and 196 m of it was on the left channel.The sand layer directly intruded into the working face in the tunnel,with the intrusive sand thickness ranging from Oto6m.
The water-rich sand stratum was simply a sand layer filled with seawater.The sea area on the Xiangan side could be divided into several parts from the surface to the construction site of the tunnel:seawater,silt,clay,water-rich sand,rock,and other layers.Normally,tunneling in the rock stratum would be the best,but the slope and direction of the tunnel could not go further down,so they had to take the challenge of the water-filled sand stratum.
Sand and soil are essentially different.With larger gaps,the sand could not retain water,or resist water.The giant sand layer is like a sponge full of seawater.”It was simply composed by sand and tiny rocks.”Su Wende pointed at the rock core sample taken from the borehole,”You see,half of it isseawater.It shows that,the water-rich sand stratum has very good permeability.It is linked directly with the sea.”
Obviously, simple excavation wouldn’t work. The tunneling could not be carried out in soft geological conditions with water. Water gushing would cause catastrophic consequences to the whole project. Technical processing would be needed with regard to the water-rich sand stratum.
But in what way would the water be pumped out? The pump could not be used to pump out the water, because the sand stratum was connected with the sea. Hu Wentao, Executive Assistant Manager of the Undersea Tunnel Project of China Railway 22nd Construction Bureau Co., Ltd. said,”There was no experience for reference. Only science would help.”That was his first time digging an undersea tunnel.
First, they thought of using a high-pressure jet-grouting pile. They planned to pile vertically on the surface of the sand stratum, to see if they could make it”denser”. They carried out over ten sets of experiments, and used the rock coring test in each experiment. It was found that the jet-grouting pile could reinforce the stratum, but it has little effect on the water shutoff, mainly because the water in the sand was affected by the tidal flow. At last, this method did not work.
However the problem had to be solved.”We thought this construction area was not particularly big. It was a few hundred meters long, and the width was limited. If we could not pump out the water directly, could we isolate the whole area, and then pump out the water from inside?”Su Wende said.
This was the scheme of “underground diaphragm wall+ well points dewatering”. After discussions, the experts believed that, as the sand stratum influence area reached 610 m, in order to ensure the safety construction and the sealing effect, the underground diaphragm wall would block the seawater’s replenishment channel to the sand stratum, and the dewatering well would dewater the sand, which would make this area meet the requirements of tunnel construction.
No sooner said than done. The workers set their feet on the shoals full of water and mud, and started the piling. The concrete walls were piled into the underground. These continuous walls were 60 cm thick, made from concrete. They were used to separate the entire sand stratum into chambers bit by bit
Then the workers set up the dewatering well to pump out the water in stages.189 deep wells were dug in this area. The water in the sand stratum would flow into these wells and be pumped out.
During the pumping, Su Wende sent the personnel to observe the dewatering well and record the water level changes every day. The data would be analyzed immediately after being summarized to guide the construction. When the pumping speed was too slow, the water level in the dewatering well would decline slowly or stop the decline, so they had to increase the density of the well from inside, or use the high-power pump. If the pumping speed was too fast, it would be too dry.The water near it would move to form a turbulent flow.
This construction lasted for several months. After the confirmation that the water level was lower than the elevation on the bottom of the sand stratum, the constructors all cheered,”We can finally dig the tunnel!”In the excavation, except some parts that saw a little water seepage because they were located in the V-shaped valley bottom, most parts were relatively dry. The scheme of “underground diaphragm wall+well points dewatering”succeeded finally.
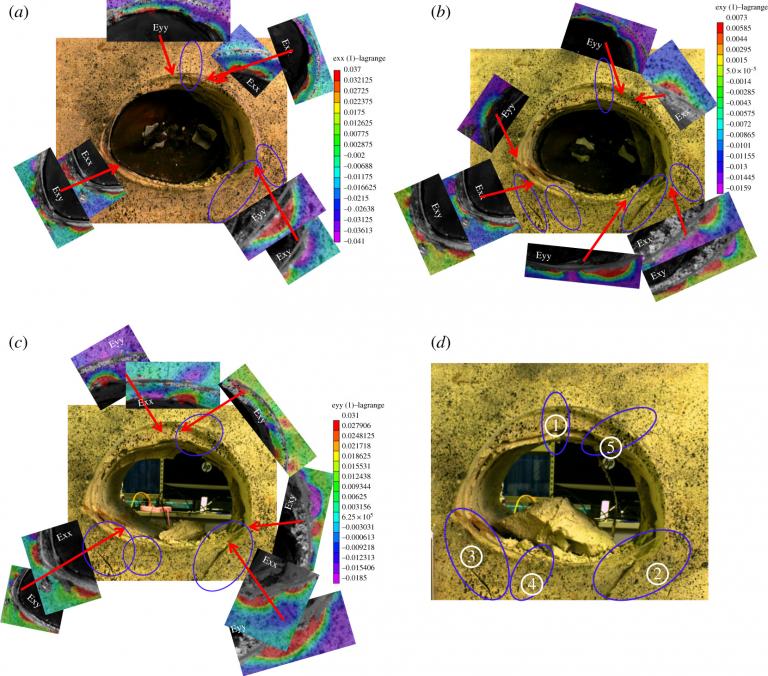